Case Study:
This case study was written for the company Engineered Recycling Systems. The study included interviewing the engineers who designed a dust collector as well as one of their customers in the paper converting industry. The customer is a company that utilizes the machine in their manufacturing process.
New Dust Collector Cuts Downtime by 80%
August 23, 2022
By Eldar Iz
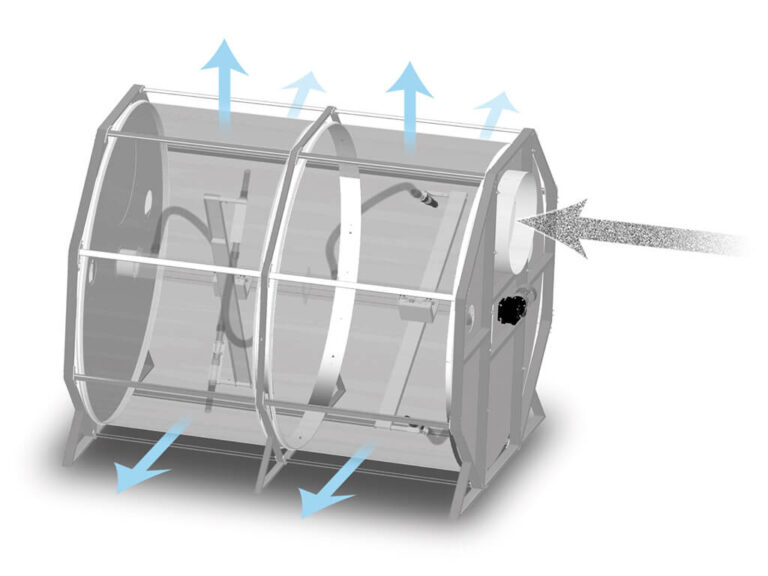
Summary
Engineered Recycling Systems (ERS) has designed a dust collector with filter media that can be replaced for under $5,000. Two people can complete the job in 2 hours, allowing production to resume. The filter can be kept indoors and has a window for monitoring the internals during operation. There are no explosion hazards so the filter does not require explosion vents.
The Challenge
Baghouse filters have long been the go-to solution for removing dust from manufacturing operations, but this type of dust collector comes with some significant downsides. It requires explosion venting, abort gates, fire protection, and demands costly downtime for maintenance procedures.
Servicing a baghouse takes a whole weekend, but many companies in the paper industry are oversold, with orders reaching as far as 2024. These businesses cannot afford to stop production for two days—and yet when the time comes to change filter media, machines are turned off and hundreds of thousands of dollars are lost while baghouses are being serviced.
“I’ve had a lot of problems in the past where they plug up on you, and you can’t get in to see what’s going on.” – Customer
The customer’s company policy doesn’t permit employees to enter confined spaces, so an outside crew had to be hired every time one of their baghouses needed inspection or maintenance.
Even when you can use in-house labor, a baghouse creates liabilities, because of the use of ladders, cranes, and not to mention, explosion vents.
After a spot fire burned down a baghouse at the customer’s facility, they decided to try a different kind of baghouse. There were some performance issues, and when it came time for maintenance, it was going to be $25,000 for the new filter media and another $10,000 for labor. This was the quarterly maintenance cost to keep the unit running correctly.
That’s when the customer started talking to Engineered Recycling Systems (ERS.) They wanted something that’s easier to service, less expensive, and not as dangerous.
This case study was featured in ‘Board Converting News’ on page 24. Click here to view the publication!
The Solution
Mike Carver, a mechanical engineer and managing partner at ERS, had just the thing: the Continuous Cleaning Modular Filter (CCM.)
“Mike showed me drawings of it and I said: ‘Yeah, I wanna try it.’ We set it all up in a weekend and started it up on Monday morning.” – The Customer
ERS designed the CCM filter so that it can be kept indoors, safe and dry. Since it isn’t boxed in, the conditions for explosion are not present. So there is no need for explosion-vents or high-speed abort gates. If the filter were to catch fire, the damage would be minimal. Since it is wide open, the only thing that would burn is the filter media itself. You would simply replace the media and be free to continue production.
ERS got it down to the point where you can change out the filter media and be back up and running in 2 hours, resulting in minimal production downtime. In-house labor can be used to do the job and it requires no special tools. Plus everything is indoors, so employees don’t need to be outside fighting the elements.
“We don’t have to pay to bring somebody else in anymore.” – The Customer
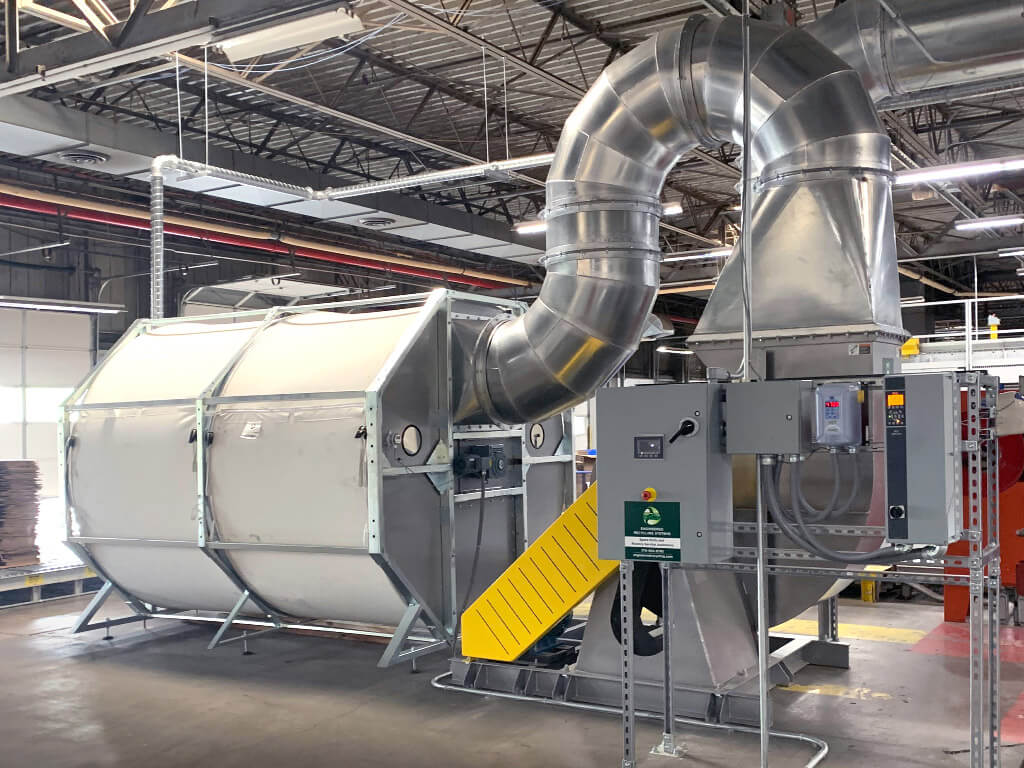
The CCM can also be safely inspected from the ground, without ladders or cranes. Unlike traditional filters, you can actually see inside the unit and monitor it, while it’s running, kind of like a see-through vacuum cleaner.
“With this filter it’s got a window on it, you can look right in it and see what’s going on. All you gotta do is walk by and you can tell if it’s working. If there’s a problem, you can see it right away. Whereas with a baghouse you’ve got no idea what’s going on inside of it.” – The Customer
The customer was instrumental in the development of the filter. They kept giving feedback and ERS kept making improvements.
“…they’ll come right in and take care of it. It’s not like he’s asking for a P.O. number. If there’s a problem, he wants to rectify it, and move forward. You don’t have to wait weeks for somebody to come in. He becomes a partner with you basically.” – The Customer
After partnering with the customer, ERS worked with a consulting firm that specializes in fire protection engineering. They worked together with an integrated compliance department to make sure the filter meets all OSHA and NFPA requirements for non-explosives. Several standard designs resulted from this, and the filter was fine-tuned to be compliant with all industry standards and local codes moving forward.
Once CCM filter sales took off, insurance companies came out to the facilities to inspect them. They approved and insured them every time. However, when some businesses tried to get the filter pre-approved before installation, insurance rejected them. This caused a few people to pull out of the purchase.
So why is the same insurance company that has already insured multiple CCMs rejecting it for pre-approval? Out-dated pre-approval policies. Many of the insurer’s pre-approval requirements were written for filters with older technology, and simply do not apply to the CCM’s specifications. Insurers need to update their policies to keep up with new industry standards.
“It meets all codes. Insurance companies have approved it across the board. I’ll argue with any insurance company and win that argument. They can’t give us an engineering reason why they wouldn’t insure it.” – Mike Carver (Engineered Recycling Systems)
The Bottom Line
The cost of owning a CCM filter is less than half the cost of owning a baghouse or cartridge-style filter. Each CCM filter is saving the customer’s company $30,000 annually on maintenance costs, but more importantly, every unit is freeing up more time for production. Servicing the filter is so quick and easy that downtime has been cut by 80%. Instead of having to hire a crew for a whole weekend, two people can now complete a preventative maintenance and filter media change in 2-6 hours, depending on the size of the unit—and it’s all indoors. No ladders or special tools required.
The best dust collector is the one you don’t have to think about. With explosion hazards out of the way, and a window to monitor the internal operation, the CCM filter is a solution that is engineered for peace of mind.
The customer’s company went on to install five more units across the Midwest, with another one in the works. There are currently more than 50—fully insured—CCM filters operating throughout the United States.
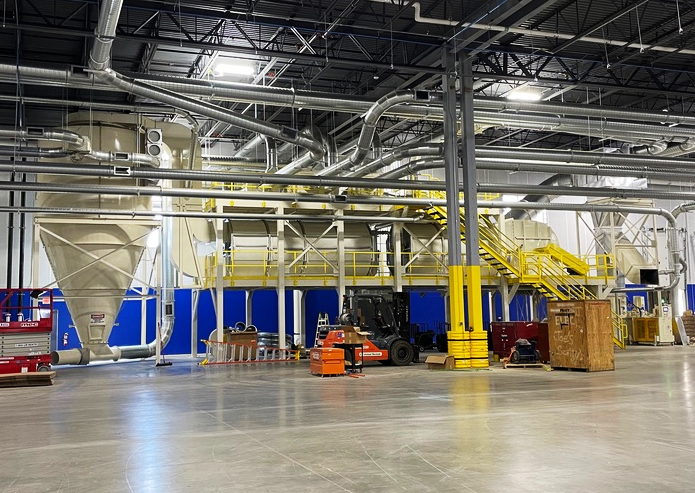
Best of all, you get quality content written by somebody who actually cares about the subject matter.

100% Money-back Guarantee*
My intention is to partner with you for the long term. I’m confident that I can create written content that ticks all the right boxes.
I’m including a money-back guarantee to show that I am committed to seeing your projects through to the highest standard. If you’re not satisfied with my work, you can ask for a full refund.
*Guarantee details are outlined in the freelance contract.
